Leiterplattentechnik
1943 ließ sich Paul Eisler, ein Wiener Elektronik-Ingenieur, das Prinzip der gedruckten Leiterplatte patentieren. Seine Idee bestand darin, die elektrischen Verbindungen der Bauelemente auf einem zweidimensionalen Träger anzuordnen. Wurden anfangs die Leiterzüge ausschließlich auf Keramikträgern gedruckt, ging man in den 1950er Jahren dazu über, die Keramik durch preiswertere Materialien zu ersetzen. Die Leitschichten –vorrangig Kupfer- wurden ganzflächig aufgeklebt und mittels Ätzen strukturiert. Dadurch gewann diese Technologie mehr und mehr an Bedeutung.
Resultierend aus der ständigen Miniaturisierung der Bauelemente und damit der geforderten höheren Verdrahtungsdichte wurden die Leiterplatten immer komplexer. Bald reichte eine Ebene nicht mehr aus und es entstanden Mehrlagenleiterplatten mit metallisierten Bohrungen. Die Metallisierung der Löcher erfolgt hierbei vorrangig in speziellen chemischen/galvanischen Bädern. Dadurch können auch im Inneren liegende Leiterzüge angebunden werden.
Parallel dazu wurden die Leiterzüge immer feiner und die Bohrlöcher immer kleiner. Wurden diese anfangs ausschließlich mechanisch eingebracht, arbeitet man heute bei kleinen Löchern verstärkt mit Lasern. Je nach eingesetztem Material sind hierbei Bohrungen kleiner 50µm möglich.
Aber auch die Basismaterialien haben sich weiterentwickelt: Es kommen heute starre aber auch flexible Polymere bei Einsatztemperaturen bis über 300°C zur Anwendung. Diese sind mit Leitschichten verschiedenster Stärke versehen - von unter 1µm bis in den mm-Bereich. Die dicken Schichten dienen gleichzeitig dazu, die Wärmeableitung der Baugruppe zu verbessern. Die Leitschichten werden aufgeklebt oder kleberlos aufgebracht.
Der Layoutentwurf erfolgt heute mittels modernster Software an leistungsfähigen Computern. Bei Bedarf kann auch das HF- sowie das thermische Verhalten der Baugruppe berücksichtigt werden.
Früher wurde das Leitbild vorrangig durch Siebdruck ätzresistenter Farben übertragen, heute kommt meist die Strukturierung von auf das Basismaterial aufgebrachten Fotolacken zum Einsatz. Das geschieht mit Hilfe von Planfilmen oder durch Laser-Direktbelichtung. Die realisierbaren Strukturbreiten betragen 20µm und kleiner.
Um die technologiebedingte Unterätzung zu minimieren, erfolgt die Herausarbeitung des Leiterbildes heute mittels modernster Sprühätzmaschinen.
Zum Schutz der Baugruppen vor Umwelteinflüssen dienen verschiedene organische Schichten sowie Metalloberflächen aus Gold, Zinn, Silber u.a.
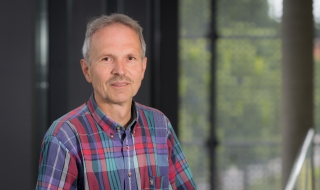
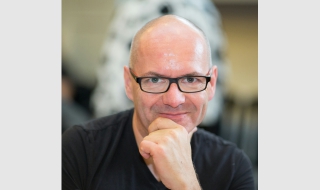