Characterization and Diagnostics
Non-destructive Testing
Non-destructive evaluation methods gain in importance in electronics packaging due to the ongoing miniaturization, increasing complexity (nano packaging), demanding conditions of application and the introduction of new materials and technologies. Ultrasonic and X-ray microscopy are evaluation methods to optimize technological processes and to characterize the geometrical behavior of packages as well as analyzing tools to investigate failure mechanisms and to interpret defects. Reliability relevant changes of materials and inside interconnecting layers as well as the development of such defects due to accelerated load can be well documented in addition to the results of destructive tests. The field of activity „non-destructive evaluation“ contains the exploitation of new application possibilities for standard processes and at the same time the development of new methods for image reconstruction and signal processing to extend and improve common techniques.
The measurement of substrates and components of electronics packaging at high resolutions is an important part of nondestructive evaluation. During the next 10 years micro- and nanoelectronics will put components on the market which will have 5000 I/Os and a pitch of 20µm. Many of today used measurement processes and equipment are already able to fit the demands concerning view field and lateral and vertical resolution and are successful used during the development of technologies and for quality management tasks. In the future it will be necessary to acquire the needed product specific data in a production environment under real-time conditions. The defect evaluation of Stacked-Die-Assemblies (e.g. System-in-Package) requires the further development of ultrasonic microscopy concerning the signal separation inside multilayer systems with thin layers. Using the full circle X-ray tomography the reachable resolution is too low for many objects of electronics packaging, e.g. modules based on large printed circuit boards. Limited-Angle-Tomography can be an alternative method. The development of simulation methods and reconstruction algorithms to adapt both investigation methods on future demands is part of the research work.
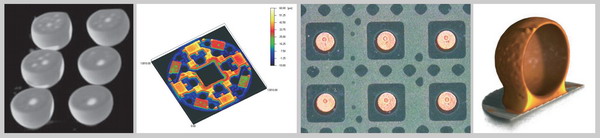
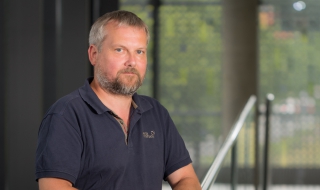
Microstructure characterization
Peter Haasen defines „microstructure as all the existing lattice defects in a metal which are not in thermodynamic equilibrium (according to type, number, distribution, size and shape)” [1]. If activated (e.g. by increased temperature during operation) these crystal defects can form undesirable changes in microstructure which affect the mechanical and electrical function. Apart from that, it is also necessary to investigate material interactions (such as interdiffusion or corrosion). In addition, the microstructure analysis is relevant to the examination of technological processes which makes it an important tool for process optimization.
[1] Haasen, P.: Chapter 3 – Microstructure and Phase, Grain- and Phase Boundaries“, In: Physical Metalurgy, 3rd Revised Edition, Cambridge University Press, 1996, S. 42, 978-0-521-55925-6 (ISBN)
Microstructure characterization and its methods will remain one of the most important process-related tools for the implementation of future technologies, and the use of new materials for electronics packaging. Moreover, it is an integral part of the physics of failure analysis for existing and future solutions in electronics packaging.
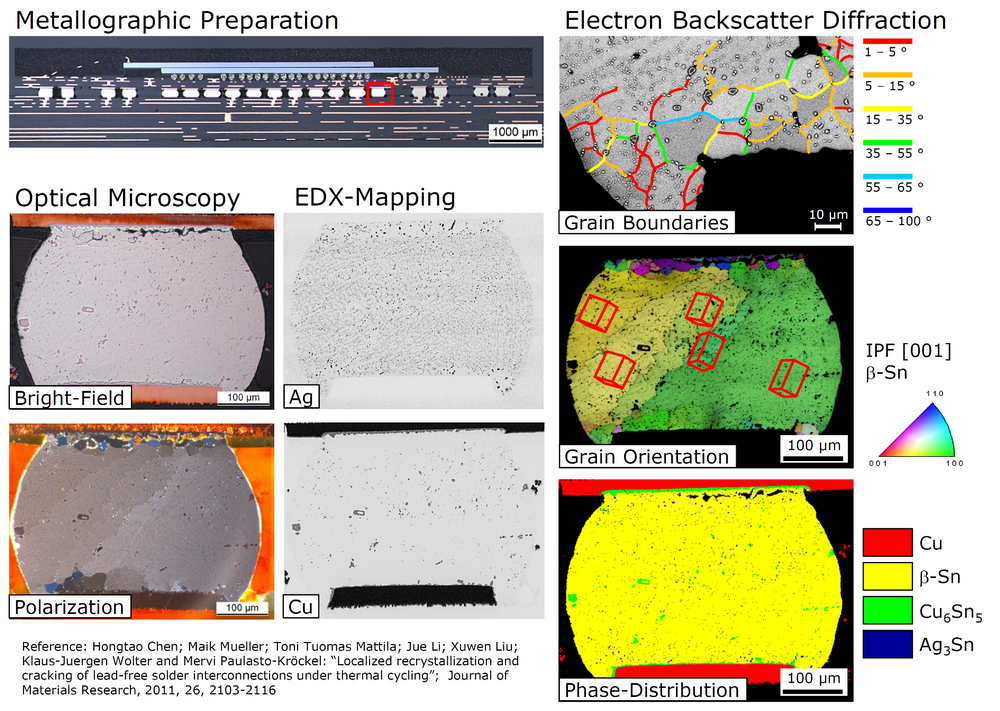
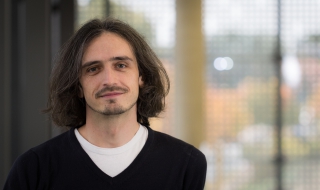